UTI In The News > |
Published
Articles > |
Proper Trencher Chain Maintenance
|
|
|
Proper Trencher Chain Maintenance: An Essential Part of Profitability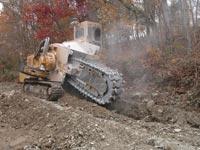
By Tim Passon
Chain-type trenchers range in size from pedestrian trenchers with a gross engine horsepower of 5 hp, to ride on, rubber tire utility-type trenchers with engine horsepower from 35 to 125 hp. Then you have pipeline digging, track trenchers with horsepower ranging from 300 hp all the way up to 1600 hp. For any type of trencher, chain maintenance is one of the keys to good performance and profitability, especially with track trenchers.
While digging conditions are a concern for all types of chain machines, track machines definitely present an entirely new set of challenges for the contractor. These monster trenchers can generate chain speeds of 700 to 1000 feet-per-minute and it would not be unusual for them to create heat up to 700 degrees Fahrenheit. With digging depths up 35 feet and cutting widths up to 60 inches, these machines are doing significantly more than putting in sprinkler systems.
When dealing with track machines first and foremost there is a distinct concern for safety. Kevin Wood from Trench Tech, recognized as one of the most knowledgeable people in the industry, told me, “Everyone one involved must be on board; you definitely have the opportunity for loss of limb during the maintenance of a track trencher.” This amplifies the most important aspect of trencher maintenance, safety. Everyone must be on the same page and follow proper maintenance procedures.
While price is very important these days, at UTI we tell customers that a quality chain, and maintaining that chain, is also very important and will help them get the most for their money. Consider that it can take two men a ten-hour day just to replace a chain and it is no picnic. With that said, it is obvious that contractors want to get as much life as possible out of their digging chain. Several simple steps can help you get the most out of your trencher chain investment.
First and probably the most important is chain tension. A rule of thumb for track trenchers is 1-inch of sag per foot of depth. While digging in dry conditions, checking tension once or twice per day is probably adequate, however in wet conditions the operator may check chain tension every hour.
Chain tension is even more critical on a mechanically driven machine. A chain that is over tightened will not allow the soil material to escape from around the tail wheel. Because of the downward pressure, the chain rides against the digging boom and the material has nowhere to escape. As the soil material starts to pack in around the chain components, it causes the chain to stretch and builds pressure on the chain links. Eventually, something has to give.
The consequence of over tightening the chain can reach far beyond simple premature wear and the need to replace it. Other components of the machine can also become over taxed or damaged. And at a cost $20,000 to $30,000 for a chain assembly, it is definitely something to prevent if possible.
Second, sprockets are very important. Some sprockets are made from a 4140 material and are thru hardened, while others are made from mild steel and only the teeth are heat treated. As a sprocket wears, the pitch of the sprocket actually changes until it no longer meshes properly with the chain rollers. The effect is premature wear to the chain rollers. When the sprocket tooth has worn down approximately ¼-inch off of the original size on the working side, it is time to change the sprocket. In the case of a 4140 thru hardened sprockets, they can be reversed and digging can continue utilizing the un-worn side.
Ultimately, there are so many variables that go into the life expectancy of a chain that it is difficult to really estimate its life span, however, it seems that 1000 to 1300 hours is a good goal. A 4140 heat-treated sprocket costs a little more, but can last as long as three chains.
Third is experience. You are most likely not going to find an inexperienced operator on a track trencher, and if you do they are sure to be accompanied by a well-trained individual. An experienced operator will pay attention to the conditions and how the machine is digging, all the while making adjustments to chain speed and chain tension.
Fourth, as with any cutting tool, it must be sharp to be most effective. Conical carbide cutting bits are generally used on track trencher applications. There are many different bits available, but it really boils down to a cap or an insert style bit. For general, all-around cutting, an insert-carbide will do the job. The fact that the carbide piece inserts about 1-inch into the bit enables it to withstand the pounding of tough conditions without losing the carbide.
A cap bit is just what it sounds like. The cap is larger diameter carbide, but does not insert into the bit. A cap bit puts more carbide on the working surface and is ideal for more abrasive conditions. When you encounter rock or more severe conditions, however, you run the risk of knocking off the carbide and basically making the bit useless.
At $15 to $22 per bit, it is very important to match the proper carbide configuration with the job. As mentioned, there are plenty of carbide tools available with different amounts of carbide content and carbide configurations, but the bottom line is that none are worthwhile if they are broke or worn out. Regular inspection and replacement of broken or worn carbide bits will pay dividends in the long run.
There are plenty of things to consider when digging with a track trencher but the bottom line is that it is very competitive out there and anything you can do to save money helps. Up time is critical. The cost of transporting one of these machines is high let alone transporting it back to the shop for a chain replacement. Make sure to work with your parts and chain vendor to ensure that you are getting the product you need for your job. That, coupled with proper care and maintenance, provides the contractor a competitive edge.
Tim Passon- Underground Tools, Inc. |